Module 1 Pig Welfare, Slaughter and Biosecurity
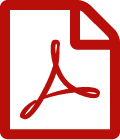
4 Abattoir biosecurity
Last Updated: 20 Mar 2024.
4.1 Cleansing of livestock vehicles
4.1.1 All assured and non-assured pig livestock vehicles entering the abattoir site shall be thoroughly cleansed and disinfected prior to leaving the site.
4.1.2 The site shall have a documented biosecurity risk assessment and associated standard operating procedures that cover the following:
- Adequacy of the cleansing and disinfection facilities for the number and types of vehicles to be cleansed and disinfected (see clauses 4.1.4 to 4.1.7)
- The number, type and size of bays required (see clauses 4.2.1 and 4.2.2)
- Flooring (see clause 4.2.3)
- Lighting requirements (see clause 4.2.4)
- Risks of cross contamination (see clauses 4.3.1 and 4.3.2)
- Drainage (see clauses 4.3.3 to 4.3.5)
- Removal and storage of manure (see clause 4.3.6)
- Access to the facilities (see clauses 4.4.1 and 4.4.2)
- Cleaning equipment and personal protective equipment (PPE) requirements (see clauses 4.4.3 to 4.4.5 and 4.6.1)
- Cleaning chemical requirements (see clauses 4.4.6 to 4.4.10)
- The methodology for cleansing and disinfecting (see clauses 4.5 and 4.6.2 to 4.6.4)
- The length of time required to effectively cleanse and disinfect each vehicle
- Cleansing inspection requirements (see clauses 4.6.5 to 4.6.10)
4.1.3 The risk assessment shall be reviewed and updated annually or after major changes to the site and aligned to the company’s internal audit programme to assess compliance against the BMPA Pig Welfare, Slaughter and Biosecurity module.
4.1.4 A dedicated, well designed and maintained area shall be provided within the site for the cleansing and disinfection of livestock vehicles. Disinfection may be carried out after cleansing, in a separate area from the washing bay if the area remains within the site boundary and movement of the vehicle to the disinfecting area does not pose any cross-contamination risks.
4.1.5 A site plan detailing the location of wash facilities and the movement of clean and dirty livestock vehicles shall be available.
4.1.6 The livestock vehicle cleansing, and disinfection facility shall be available to drivers when their vehicles are on site.
4.1.7 Where there is insufficient space on the site to provide, adequate vehicle wash facilities the charter participant shall seek derogation from the BMPA PTAC. Each derogation request will be assessed on a case-by-case basis but will be viewed as a last resort. Off-site facilities, if approved by PTAC shall be local to the abattoir and under the management of the charter participant. All other requirements of Section 4 shall be met in full.
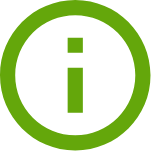
Guidance
For further guidance see Appendix 1 of this module.
Access to the facilities shall be available when pigs are being delivered to the site. Livestock vehicles shall have unrestricted access to the facilities following unloading of pigs and the charter participant shall ensure that there is no excessive back log of vehicles waiting to be cleansed (access within 1 hour of unloading should be used as a guide).
The design of the facilities shall be such that it eliminates any potential damage to services/equipment e.g. water taps/pipe work during the movement of transport within the general area.
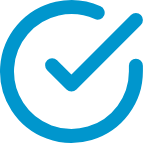
Evidence
Review evidence of livestock vehicle deliveries against vehicle lorry washing inspection reports. Review risk assessment and standard operating procedures (SOP`s) for compliance to the charter.
Visual inspection of facilities. Verification that the area is dedicated for the cleansing and disinfection of livestock vehicles and is available always. Site plan detailing location of wash facilities and the movement for clean and dirty livestock vehicles. Where vehicles are cleansed off site evidence of derogation from the PTAC shall be checked.
4.2 Wash bays
4.2.1 The charter participant shall have sufficient number and size of wash bays to allow effective cleansing and disinfection of all vehicles at peak periods, without excessive delay and prior to the vehicles leaving site.
4.2.2 Bay(s) may be ‘drive-through’ but where this is not possible, the site shall provide clear SOP`s to ensure that the area immediately in front of the bay is cleansed and disinfected before vehicles are driven out.
4.2.3 The floor of the bay shall be hard standing, well maintained and slope away from the vehicle so that washout water free-flows away from the tailboard and wheels towards the drain.
4.2.4 Sufficient lighting shall be provided to ensure that each wash bay, including the interior and exterior of the vehicle, is adequately lit so that effective cleansing, disinfection and inspection can be carried out regardless of the time of day/night.
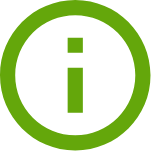
Guidance
The participant shall have considered the different types and sizes of vehicles used to deliver livestock. Regarding 4.2.4 (lighting) It is not the intention to prescribe the minimum lux level. The HSE recommends 20 lux for outdoor work involving movement of lorries, however it is expected that the site shall have taken into consideration the design, location, and time of operation of the vehicle wash facilities as this shall vary from site to site.
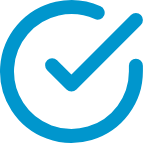
Evidence
4.2.1 Visual inspection of area. Verify by cross checking examples of delivery vehicle types against the risk assessment study. The check shall include the length of vehicle against actual length of bay. Bays shall be appropriate in length to type of vehicle. Look for evidence of excessive back log of vehicles waiting to be cleansed (max 1hr delay as a guide).
- For bays that are not ‘drive through’, verification may be sought from:
- visual inspection of bay area
- copy of work instructions
- discussion with livestock vehicle driver
4.2.3 Visual inspection of floor area within the bay area. Verify the direction of the flow of water within the bay drainage area.
4.2.4 Verification of location, number of lighting units and operation of lighting provided. The auditor shall review supporting evidence within the checklist e.g. checking the number of lighting units and verification that all the light units in the wash bay area are working.
4.3 Preventing cross-contamination of wash bays
4.3.1 The facilities shall be designed and supported by standard operating procedures (SOP`s) that ensure effective cleansing, disinfection and which prevent cross contamination between dirty water, manure, personnel, personal protective equipment (PPE), equipment and vehicles.
4.3.2 Where more than one wash bay are provided, a system to prevent cross contamination between bays shall be in place.
4.3.3 There shall be a protected drain area towards one end of each bay that is positioned behind the open tailgate of all vehicles that use the facility.
4.3.4 The drains shall ensure the contaminated wash-out water is routed towards a suitable containment tank to facilitate proper disposal, or to the main sewer, where on site facilities and legislation permit.
4.3.5 The site shall demonstrate appropriate disposal of wash-out water from the containment tank. The site shall also hold a drainage plan to indicate the flow of wash out water.
4.3.6 Facilities shall be provided for the storage of manure/debris to prevent cross contamination before removal from the site.
4.4 Cleansing and disinfection facilities
4.4.1 The cleansing and disinfection facilities shall be clearly identified, appropriate for their intended use and, where there is more than one, be specific to each wash bay.
4.4.2 Adequate storage facilities shall be provided for cleaning equipment, personal protective equipment (PPE) and chemicals.
4.4.3 Adequate equipment and (PPE) shall be provided, be appropriate for its intended use and be well maintained for each vehicle wash bay.
4.4.4 A list of equipment and PPE provided shall be readily available to livestock vehicle drivers.
4.4.5 The hose reels, pressure washers and disinfectant facilities shall be protected from temperature extremes to ensure effective wash-down operations can continue throughout winter weather.
4.4.6 Sites and livestock vehicle drivers shall comply with current health and safety legislation.
4.4.7 DEFRA approved disinfectants shall be supplied by the site at the vehicle wash facilities.
4.4.8 Control of Substances Hazardous to Health (COSHH) data shall be held by the site for the chemicals provided.
4.4.9 The disinfectant and detergents shall be diluted and utilised in full accordance with SOP`s and the manufacturer’s instructions.
4.4.10 In compliance with current health and safety legislation chemical shall be securely stored to prevent unauthorised access or cross contamination with food, raw materials and packaging.
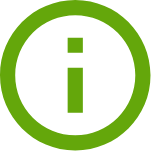
Guidance
The cleansing and disinfection facilities shall be readily identified by colour, design or signage.
Copy of cleaning manual and availability to livestock drivers, list of equipment and PPE. Verification of condition of equipment and personal protective equipment and storage facilities for hose reels etc.
The site shall have taken into consideration the following:
- appropriateness of the system for the application of the cleaning chemicals during the cleaning operation
- how the cleaning chemicals are to be supplied to the wash facilities safely (where the chemicals are to be dispensed)
- storage facilities when cleaning chemicals are not in use
- the site shall have developed appropriate work instructions for the dilution of chemicals. Work instructions shall be readily available
A list of DEFRA approved detergents and sanitisers shall be reviewed and this should list the chemicals in use http://disinfectants.defra.gov.uk/DisinfectantsExternal/default.aspx?Module=ApprovalsList_SI. However, it should be noted that DEFRA frequently update the list, so it is possible for a chemical to be on the list at the time of purchase to be then removed at a later stage whilst the chemical is still in use at the site. In such circumstances if the site can prove the chemical was on the list at the time of purchase and that arrangements are in place to move to a chemical on the updated approved list at the next re-order point then this would be viewed as being compliant to the charter requirements.
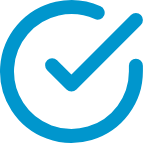
Evidence
Verification shall be sought for the following:
- evidence of training that includes health & safety legislation (where appropriate)
- detergents and disinfectants are supplied to the wash facilities in accordance with legislation
- availability of up to date COSHH data sheets covering the scope of cleaning chemicals manufacturer’s recommendations in relation to dilution rates aligned to legislation.
- correct storage of chemicals
4.5 Standard operating procedure (SOP) for cleaning
4.5.1 The site shall have a documented standard operating procedure (SOP) for the cleansing and disinfection of livestock vehicles.
4.5.2 The SOP shall have, as a minimum, five distinct stages of cleansing:
- dry removal of all solid manure including straw or shavings
- detergent soaking stage
- wash stage using pressurised clean water
- application of disinfectant to all cleaned, drained surfaces
- inspection
In addition, the following shall be clearly stated:
- methodology of cleansing to include disinfection
- frequency of cleansing
- cleaning chemicals to use
- dilution rates
- contact times
- safe use and storage of cleaning chemical
4.5.3 Detergent and disinfectant shall be applied in methodical and overlapping horizontal or vertical sweeps to ensure that all surface areas are covered. Detergent shall be applied using a foaming lance and allowed at least 10 minutes contact time to be effective
4.5.4 The SOP shall detail the staff duties and responsibilities for the maintenance and cleanliness of facilities.
4.5.5 To cover for staff leave, the site shall have a minimum of two named contacts with responsibility for the maintenance and cleanliness of the vehicle wash facilities. The names and contact details of the nominated individuals carrying out this task shall be displayed at the washout facilities. The named staff shall demonstrate competence aligned to their responsibilities.
4.5.6 The SOP shall be reviewed and updated at least annually.
4.5.7 The standard operating procedure for effective use of the vehicle wash and the cleansing and disinfecting of the vehicle shall be communicated to livestock vehicle drivers at the wash bay.
4.5.8 Operating procedures for the use of detergents and disinfectants (including the PPE to be worn) shall be clear, unambiguous, and displayed in an accessible position at the wash bay.
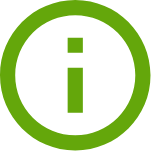
Guidance
See Appendix 1 of this module for guidance on auditing technique which refers to the recommended wash process in the ‘Effective Cleansing of Livestock Vehicles’ report, on page 17 and for audit point locations, refer to Appendix (i) of the report on page 19.
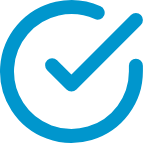
Evidence
Copy of SOP for cleansing and disinfection of livestock vehicles. Verification of methodology aligned to clause 4.5.3. Visibility of named personnel displayed in washout facilities and demonstration of competency. Evidence of last review date of SOP and amends.
Displayed copy of SOP and verification of livestock vehicle driver’s awareness of SOP and inspect the standard of vehicle cleansing and disinfection.
4.6 Livestock vehicles and drivers
4.6.1 All livestock vehicle drivers shall be instructed on the correct use of the wash bay, equipment, personal protective equipment (PPE) and its location.
4.6.2 Livestock vehicle drivers shall, within an hour be given sufficient time to effectively cleanse and disinfect their vehicles before leaving site.
4.6.3 It is the responsibility of the driver to ensure each wash bay and PPE is cleaned down and the PPE disinfected, hoses are rolled up and the bays are left clean and tidy after use.
4.6.4 The site shall provide drivers with the opportunity to comment on the facilities provided. Any complaints shall be treated in accordance with the site’s complaints procedure.
4.6.5 The abattoir shall hold an up to date list of all livestock vehicles entering and leaving the site.
4.6.6 All livestock vehicles shall be inspected by appropriately trained site-based personnel prior to the vehicle leaving site. To verify that livestock vehicles are being maintained in good condition and cleansed and disinfected in accordance with the site’s standard operating procedure (SOP).
4.6.7 The site shall develop a checklist that covers the scope of the SOP for the condition, cleansing and disinfection of livestock vehicles. The checklist shall be completed in full to include name of the driver, details of the vehicle including its registration number, condition, time into and out of wash bay and the name of the person carrying out the vehicle inspection and whether the standard was acceptable or not.
4.6.8 Where inspection identifies an issue relating to cleanliness, the vehicle shall be re-cleansed and disinfected to the appropriate standard before it can leave the site. Issues associated with vehicle condition shall be reported to the driver. Root cause and corrective action shall be established and recorded. Recurring issues shall be reported to senior management and to the assured livestock transport scheme body.
4.6.9 Records of vehicle inspections and corrective actions shall be held on file and form part of the completed vehicle inspection checklist.
4.6.10 The site shall have a named person onsite that is responsible for ensuring there are regular verifications in place to ensure all vehicles leaving site are suitably cleansed and disinfected.
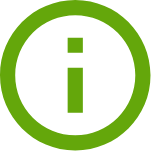
Guidance
4.6.2 The site shall have considered this requirement within their risk assessment exercise. Approximate times shall be documented dependent on vehicle type and size within the risk assessment.
The ‘Effective Cleansing of Livestock Vehicles’ report in Appendix 1 of this module suggests that the following vehicle cleansing times are required:
- Artic (triple deck) 2 ¼ hours
- Drawbar combination (double deck) 2 hours
- Rigid (triple deck) 1 ¾ hours
4.6.5 Information of livestock vehicles, cleansing records shall already form part of the site’s data base for monitoring pig deliveries aligned to animal movement documents.
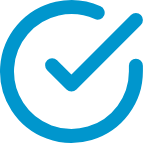
Evidence
4.6.1 Training records of livestock vehicle drivers. Copy of cleaning manual and availability to livestock drivers, list of equipment and PPE.
4.6.2 Record time of a clean down. Discussion with livestock vehicle driver on time and expectation of cleansing time.
4.6.3 Visual inspection of bays for good manufacturing practice (GMP). Review examples of completed feedback questionnaires since the last audit. Review responses aligned to sites complaints procedure and where appropriate evidence of corrective action undertaken.
4.6.5 Review vehicle inspection records and evidence of how issues are resolved.