Module 4 Ham & Cooked Pork
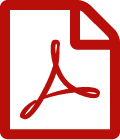
6 Injection and curing procedures
Last Updated: 6 Jan 2022.
6.1 The injection process
6.1.1 There shall be standard operating procedures, and work instructions in place for the operation and management of the injection process.
6.1.2 The product temperature during preparation process may be 0°C to +5°C. If this is exceeded it shall not exceed +8°C and shall return to <5°C within 4 hours.
6.1.3 The product temperature during the injection process shall be 0°C to +5°C.
6.1.4 Injection gains shall be monitored, recorded and checked against specified “pick-up” targets for each batch of pork being processed by weight checks measured pre and post-injection on a specified number of products.
6.1.5 Checks shall be carried out on the injection needles before injection commences to verify that needles are intact and there is no blockage of the needles that could result in ‘mis-cure’.
6.1.6 Where non-conformance occurs, the site shall investigate root cause and implement corrective action.
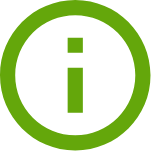
Guidance
Appropriate recipes and work instructions shall be in place and detail the required criteria for the range of products produced on site. It is acknowledged that customers own brand label products may determine the recipe formulation.
Whilst the legal maximum temperature limit for meat in process is <8°C EHO`s tend to give some flexibility which maybe reflected by the approach taken by the auditor i.e. if temperatures of >8°C are seen but there is clear evidence that product temperatures are returning to <8°C within 4hours of final packing then it would be appropriate to raise this as an observation, however if the product temperature was still at higher than 4°C 4hours after final packing then this shall be viewed as a minor non-conformance.
Irrespective of the recipe formulation, in-process checks shall be undertaken to monitor the product temperature up to the point of filling. Records of temperatures shall be held.
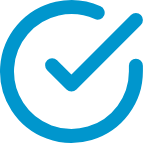
Evidence
Documented procedures, recipes and work instructions for the operation and management of the injection process. Examples of product temperature records, injection gains and checks on needle integrity and evidence of record keeping where corrective action was undertaken.
6.2 Curing procedures: Category 1 – Dry cured ham
6.2.1 The raw pork material being cured shall be in the form of either whole bone-in legs, legs which have been partly or completely boned, or individual leg muscles which are subsequently reassembled before cooking.
6.2.2 Curing shall be carried out by using dry ingredients. Permitted additives (caramelised syrups, honey, purees and sauces) may be added after the dry cure application.
6.2.3 The pork muscles, if cured individually or in groups, shall be restricted to the following major muscles- topside, silverside, thick flank, chump or muscles from the oyster region (but excluding the primary hock) of the leg. Single or mixtures of all five muscle types may be used to form the ham.
6.2.4 The curing mixture shall be applied dry to all accessible surfaces of the meat.
6.2.5 Dry-cured ham may be cured in a variety of ways but only using only those ingredients listed in clause 5.2.1 and 5.2.2.
6.2.6 Whole boneless legs or individual muscles may be massaged or tumbled during the curing process, but this shall not cause significant breakdown of the pork.
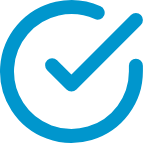
Evidence
Documented procedures, work instructions, recipes and in- house specifications for the operation and management of the process. Examples of production records since the last audit Visual inspection of product to verify adherence to specification.
6.3 Curing procedures: Category 2 – Traditionally cured Wiltshire ham or ham hock
6.3.1 Pork Legs intended for Wiltshire curing shall be either cured on the side, part-side, or as individually butchered legs or associated muscles.
6.3.2 Ham Hock (comprising of primary and/or secondary shank as defined within Appendix 1) shall be slow cooked to breakdown the gristles and sinews associated with these cuts.
6.3.3 The injection and cover brine shall only contain salt (NaCI), sodium or potassium nitrite and/or sodium or potassium nitrate.
6.3.4 Injection may be carried out manually or by multi-needle injection.
6.3.5 It is a characteristic feature of Wiltshire curing that the live cover brine shall be re-used continually. Therefore, standard operating procedures, work instructions and records shall be in place that state the compositional targets and tolerances (salt, nitrate, nitrite, pH & temperature), and actions to be taken when these fall outside of stated limits, so that the condition of the live cover brine can be maintained and where necessary corrected. All actions and brine amendments shall be recorded.
6.3.6 A starter culture shall only be used in the conception of the fresh immature live cover brine. At conception, the brine shall be regularly aerated and checked to ensure that the starter culture is active and that the condition of the brine is developing. To facilitate development the immature live cover brine shall be used to cure products for at least two months before it can be used to manufacture product that can be certified as BMPA Quality Assured Ham and Cooked Pork.
6.3.7 Over time the volume of live cover brine will deplete so occasional “top-up” using a freshly prepared brine incorporating a starter culture may occur. The mother brine to which the “top-up” brine has been added can continue to be used on the condition that the “top up” brine shall not exceed 25% of the mother batch of live cover brine.
6.3.8 Live cover brines not in regular use shall be regularly aerated and condition monitored to maintain its condition.
6.3.9 A recorded log of cover brine history, top-ups, and adjustment shall be maintained to demonstrate composition and provenance.
6.3.10 Pork shall be fully immersed in the live cover brine for a minimum period of a 3 days (72hours).
6.3.11 After immersion, and prior to further processing, the cured sides/pork cuts shall be allowed to drain and then matured in air at +2°C to +5°C for a minimum of 96 hours (4days) and to a clearly specified maximum time that shall be validated using shelf life and food safety.
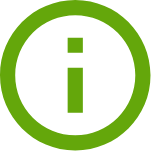
Guidance
In a Wiltshire-curing system, the objective is to maintain the live cover brine in a stable condition with a predictable and controlled rate of conversion of nitrate to nitrite.
Brines used in different plants vary in their behaviour due to differences in their micro flora and this behaviour must be recognised. Because of their singular nature a unique characteristic is that the live brine is continually re-used. The practice of freshly and routinely preparing the live cover brine by the addition of a starter culture is a modern short cut intended to circumvent the traditional time aged process and is not compliant with the requirements of Clause 6.3 that is specific to the traditional process. To be certified by the charter such products, for the purpose of labelling and differentiation from authentic and traditionally Cured Wiltshire Ham and Ham Hock, should be clearly described as “Wiltshire-Style” (or similar) within the legal name of the product. Such products, depending on the final water content of the finished product would either fall with the definition of a Category 3: Ham with No Added Water (see Clause 6.4) or Category 4: Ham with Added Water (see Clause 6.5).
The function of the starter culture is to ensure that the right microbiological flora is present in order for the live brine to mature to a point where it can be self-maintaining with occasional additions of salt, nitrite and nitrate to maintain its condition. Typical levels of microflora are of a count greater than 106 and are predominantly made up of large concentrations of micrococci and lactobacilli. Once the mature live cover brine has been created the brine can then be re-used without further addition of the starter culture, except for occasional top-up as explained below.
There will be occasions when existing cover brines will need to be replenished by the addition of a top-up cover brine normally created by using a starter culture – this should be an occasional practice rather than routine.
Immersion forms an essential part of the Wiltshire process. In Wiltshire curing, the relative concentrations of the injection and live cover brines result in a net withdrawal of water from the pork during curing because the concentration of salt in the injection brine is considerably less than that of the live cover brine.
The pH of a live cover brine is usually stable and typically falls within a range of 5.0 to 6.9. The pH value may be checked whenever brine is being re-strengthened and live cover brine with pH outside this range may be used if the charter participant can demonstrate that the brine remains stable (different starter cultures can create different pH levels). Occasional peaks outside of the set limits would not be an issue if the charter participant is monitoring the pH trends and take corrective action when non-typical pH profiles emerge. A gradual and persistent rise in the pH value indicates that the brine is becoming unstable and a critical situation will arise if this goes above 6.9, when off-odours will develop. The rise in pH is usually accompanied by an increase in the nitrite level, as a more rapid reduction of nitrate occurs.
Temperature-control plays a vital part in the production of cured pork. In most of the curing systems used commercially the operations are performed at +2°C to +5°C.
Wiltshire-cured legs are frequently stored in an unprotected form. Excess surface brine drains off (the use of hooks, racks, or slatted trays/dolavs are acceptable if free drainage can be demonstrated) and the lean and fat become firmer in texture and noticeably drier. These changes are concerned with the gelling of the water/salt/protein complex formed within the meat during curing and a gradual hardening of the fat as the crystallizing process continues after slaughter.
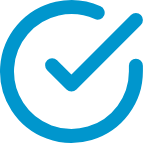
Evidence
Examples of records to be reviewed since the last audit shall comprise:
- Live cover brine composition
- Log of cover brine history, adjustments and “top-up” to demonstrate provenance.
- Temperature monitoring
- Shelf life and food safety analysis
- Appropriate work instructions
6.4 Curing procedures: Category 3 – Ham with no added water
6.4.1 Curing may be carried out on either whole bone-in or boneless leg, or on selected leg cuts/muscles (see clause 6.4.2.
6.4.2 The pork cuts/muscles if cured individually or in selected groups shall i be obtained from the major leg muscles; topside, silverside, thick flank and/or secondary hock.
6.4.3 Individual cuts/muscles may be separated for subsequent reassembling.
6.4.4 Ham with no added water may be cured in a variety of ways but is restricted to only using those ingredients listed in clause 5.2.1 and 5.2.2.
6.4.5 Whole legs or their associated cuts/muscles may be massaged or tumbled during the curing process, but this process shall not cause significant breakdown of individual muscles.
6.4.6 The ham may be dressed with added sheets of rind and/or back fat. and be cooked in tight netting, casings or presses to ensure adequate adhesion.
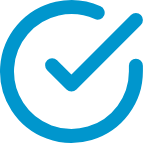
Evidence
Documented procedures, work instructions, recipes and in- house specifications for the operation and management of the process.Examples of production records since the last audit Visual inspection of the process.
6.5 Curing procedures: Category 4 – Ham with added water or ham hock (max 20% added water)
6.5.1 Curing may be carried out on either whole bone-in or boneless legs, or on selected leg cuts/muscles (see clause 6.4.2.
6.5.2 The pork cuts/muscles if cured individually or in selected groups shall be obtained from the major leg muscles; topside, silverside, thick flank and/or secondary hock.
6.5.3 Individual cuts/muscles may be separated for subsequent reassembling.
6.5.4 Whole legs or their associated cuts/muscles may be massaged or tumbled during the curing process, but this process shall not cause significant breakdown of individual muscles.
6.5.5 Ham with no added water may be cured in a variety of ways but restricted to only using those ingredients listed in clause 5.2.1 and 5.2.2.
6.5.6 The ham may be dressed with added sheets of rind and/or back fat. and be cooked in tight netting, casings or presses to ensure adequate adhesion.
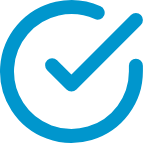
Evidence
Documented procedures, work instructions, recipes and in-house specifications for the operation and management of the process. Examples of production records since the last audit Visual inspection of the process. Verification by analysis is covered under clause 9.2.
6.6 Injection procedures: Category 5 – Cooked pork with no added water
6.6.1 Any pork cuts may be used.
6.6.2 Individual muscles may be separated before processing for subsequent reassembly.
6.6.3 Cooked pork may be processed in a variety of ways but shall only use those ingredients listed in clause 6.1.4.
6.6.4 Individual muscles may be massaged or tumbled but this shall not cause significant breakdown of individual muscles.
6.6.5 The pork may be dressed with added sheets of rind and/or back fat. and be cooked in tight netting, casings or presses to ensure adequate adhesion.
6.6.6 Injection solutions may be used but the cooking process shall be sufficient to ensure that no added water remains in the finished product.
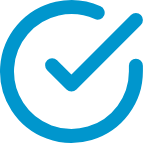
Evidence
Documented procedures, work instructions, recipes and in- house specifications for the operation and management of the process.Examples of production records since the last audit Visual inspection of the process. Verification by quality assessment is covered under clause 9.2.1.
6.7 Injection procedures: Category 6 – Cooked pork with added water
6.7.1 All requirements as stated in Category 5 shall be met (see clause 6.6).
6.7.2 In addition, injection solutions may be used but cooking yields shall ensure that the maximum added water retained in the finished product does not exceed 20%.
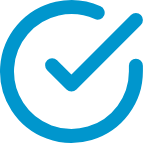
Evidence
Documented procedures, work instructions, recipes and in- house specifications for the operation and management of the process.Examples of production records & yields. Visual inspection of the process. Verification by analysis is covered under clause 10.